sábado, 31 de diciembre de 2011
viernes, 30 de diciembre de 2011
Deck
Laminado de cubierta
Materiales:
- Carbono unidireccional 200g
- Refuerzos de Aramida 200g
- Tejido de vidrio 200g
Del centro hacia el exterior, está dispuesto de la siguiente manera.
Dos tiras de carbono unidireccional de 130x30cm cruzadas de banda a banda desde popa hacia proa a la altura de la caja de mástil, pasando por encima de los pisantes traseros y delanteros, lo que da doble capa de carbono cruzado en ángulo sobre la zona entre footstraps.
Una tira de carbono unidireccional de 30cm de ancho dispuesta logitudinalmente abarcando la zona de la caja de mástil hasta el laminado anterior de carbono.
Refuerzos de carbono con los recortes de lo anterior para las zonas "blancas" resultantes de los laminados anteriores, es decir, triángulos a los costados en los cantos entre footstraps siguiendo la dirección cruzada de los laminados adyacentes y en popa, este último caso longitudinalmente, paralelo al eje de crujía..
Refuerzo de tejido de aramida en proa, en los cantos de proa y popa, y zona de footstraps delanteros.
Laminado parcial desde proa hasta abarcar y pasar la caja de mástil, montando sobre el carbono, con acabado semicircular, en tejido de vidrio 200g.
Laminado completo en tejido de vidrio 200g.
Pequeño refuerzo de tejido de vidrio en popa.
Como casi siempre, variaciones sobre la marcha. La idea inicial incluía otros gramajes de vidrio, alguno incluso ya preparado, pero las tabla y las ideas han ido evolucionando sobre la marcha y quise darle más consistencia en el último momento.
El método ha consistido en impregnar todos los tejidos y refuerzos sobre la mesa para posteriormente trasladarlos a la tabla en el orden anterior. Todos, excepto el último laminado completo exterior, que impregné sobre la tabla directamente tras colocarlo sobre los anteriores tejidos ya laminados.
Existe el riesgo, y casi la certeza, en caso de preimpregnar este último laminado sobre la mesa, de que al colocarlo sobre los anteriores tejidos en la tabla y orientar y pegar correctamente el tejido a los ya colocados, arrastre y levante consigo los anteriores, descolocándolos, y aún pudiendo hacerse con cuidado no merece la pena el esfuerzo y paciencia a tener respecto a la "posible" ventaja. Además, el impregnar este último laminado sobre la tabla asegura y refuerza los laminados inferiores.
En cualquier caso, y como siempre, hay diferentes maneras de actuar.
Materiales:
- Carbono unidireccional 200g
- Refuerzos de Aramida 200g
- Tejido de vidrio 200g
Del centro hacia el exterior, está dispuesto de la siguiente manera.
Dos tiras de carbono unidireccional de 130x30cm cruzadas de banda a banda desde popa hacia proa a la altura de la caja de mástil, pasando por encima de los pisantes traseros y delanteros, lo que da doble capa de carbono cruzado en ángulo sobre la zona entre footstraps.
Una tira de carbono unidireccional de 30cm de ancho dispuesta logitudinalmente abarcando la zona de la caja de mástil hasta el laminado anterior de carbono.
Refuerzos de carbono con los recortes de lo anterior para las zonas "blancas" resultantes de los laminados anteriores, es decir, triángulos a los costados en los cantos entre footstraps siguiendo la dirección cruzada de los laminados adyacentes y en popa, este último caso longitudinalmente, paralelo al eje de crujía..
Refuerzo de tejido de aramida en proa, en los cantos de proa y popa, y zona de footstraps delanteros.
Laminado parcial desde proa hasta abarcar y pasar la caja de mástil, montando sobre el carbono, con acabado semicircular, en tejido de vidrio 200g.
Laminado completo en tejido de vidrio 200g.
Pequeño refuerzo de tejido de vidrio en popa.
Como casi siempre, variaciones sobre la marcha. La idea inicial incluía otros gramajes de vidrio, alguno incluso ya preparado, pero las tabla y las ideas han ido evolucionando sobre la marcha y quise darle más consistencia en el último momento.
El método ha consistido en impregnar todos los tejidos y refuerzos sobre la mesa para posteriormente trasladarlos a la tabla en el orden anterior. Todos, excepto el último laminado completo exterior, que impregné sobre la tabla directamente tras colocarlo sobre los anteriores tejidos ya laminados.
Existe el riesgo, y casi la certeza, en caso de preimpregnar este último laminado sobre la mesa, de que al colocarlo sobre los anteriores tejidos en la tabla y orientar y pegar correctamente el tejido a los ya colocados, arrastre y levante consigo los anteriores, descolocándolos, y aún pudiendo hacerse con cuidado no merece la pena el esfuerzo y paciencia a tener respecto a la "posible" ventaja. Además, el impregnar este último laminado sobre la tabla asegura y refuerza los laminados inferiores.
En cualquier caso, y como siempre, hay diferentes maneras de actuar.
El resultado antes de embolsar:
A partir de la foto, con todos los tejidos ya laminados, se dispone el tejido pelable a toda la cubierta asegurado con cinta, manta de absorción sobre este, que en este caso, la mant además de ayudar a la distribución del vacío, actuará como tal recogiendo el exceso de resina.
Embolsado, y vacío a -0,4.
Se observa en la última foto como la manta va recogiendo el exceso de resina en forma de puntos que ha atravesado el tejido pelable.
Como nota, hay que señalar que para cortar y preparar la aramida son necesarias unas tijeras profesionales. Las tijeras "normales" y el cutter son insuficientes para conseguir cortarla. Es una fibra realmente fuerte. No se usa en los chalecos antibalas por casualidad.
Por lo demás, una brocha y una paleta son suficientes para trabajar la resina epoxi, siendo la brocha útil para los cantos y el solape del tejido en carena.
Una máscara de protección con el filtro adecuado es indispensable como protección. Guantes desechables, para las manos.
martes, 27 de diciembre de 2011
Wood
Laminado de carena
Materiales:
-Refuerzos de carbono para las cajas
-Tejido de fibra de vidrio 200g
-Lámina de madera de sapelly 0,6mm
En el caso del tejido de carbono he utilizado dos recortes triangulares de carbono unidireccional, que he dispuesto cruzado. Tras este, el tejido de fibra de vidrio, previamente medido y recortado, con algo de margen para sopalar el canto.
Por último, una lámina de madera de sapelly en 0,6mm. como capa final.
En este caso hay que preparar la lámina antes de pasar al propio laminado, pues las madera viene suministrada en rollos de 25cm de ancho, que hay que empalmar para cubrir el ancho de la carena.
Para la lámina de sapelly es necesario impregnar la cara interna con resina espesada. Posteriormente, es colocada sobre el anterior laminado y fijada con cinta.
Tejido pelable reutilizado, para afirmar mejor las capas dispuestas y a fin de proteger el posible traspaso de resina a través de la madera y los cantos
Manta de absorción. En este caso utilizada más como distribuidora de vacío y para aislar la bolsa que para atrapar resina, dado que debido al tipo de laminado prácticamente no actuará como tal.
Detalle de cantos, con el solape del tejido, y madera que monta sobre estos que hay que lijar y repasar
Materiales:
-Refuerzos de carbono para las cajas
-Tejido de fibra de vidrio 200g
-Lámina de madera de sapelly 0,6mm
En el caso del tejido de carbono he utilizado dos recortes triangulares de carbono unidireccional, que he dispuesto cruzado. Tras este, el tejido de fibra de vidrio, previamente medido y recortado, con algo de margen para sopalar el canto.
Por último, una lámina de madera de sapelly en 0,6mm. como capa final.
En este caso hay que preparar la lámina antes de pasar al propio laminado, pues las madera viene suministrada en rollos de 25cm de ancho, que hay que empalmar para cubrir el ancho de la carena.
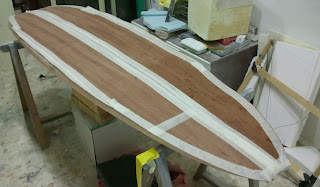
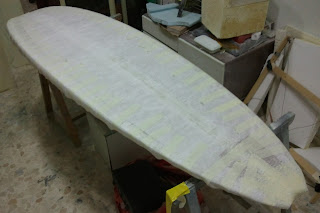
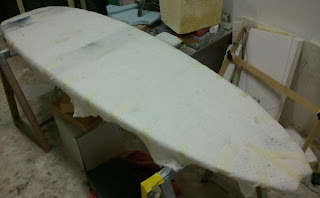
Embolsado y vacío a -0,425...
Resultado, recién desembolsado, a falta de volver a coger la lija
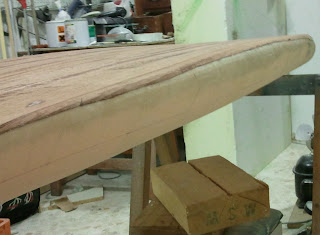
miércoles, 21 de diciembre de 2011
Aletas K4
Me ha llegado un juego de aletas de K4. Dos aletas twin 16 más dos pequeñas laterales de 8, que hacen un área de 344.
A primera vista muy buena impresión, y el material con el que están modeadas (OptoFlex) parece resistente ante golpes y roces, con buena flexión. El talón cónico de las pequeñas viene justo para las cajas, con fácil solución lijando un poco éstas.
Ya contaré más cuando toquen el agua.
Habrá que pensar en un diseño para la carena que vaya a juego con el color...parece que combinará bien con el sapelly (caoba de Guinea).
A primera vista muy buena impresión, y el material con el que están modeadas (OptoFlex) parece resistente ante golpes y roces, con buena flexión. El talón cónico de las pequeñas viene justo para las cajas, con fácil solución lijando un poco éstas.
Ya contaré más cuando toquen el agua.
Habrá que pensar en un diseño para la carena que vaya a juego con el color...parece que combinará bien con el sapelly (caoba de Guinea).
martes, 13 de diciembre de 2011
Twin...Quad (2)
Segunda parte de la colocación de las cajas para las aletas laterales.
Hay diferentes maneras de colocar una caja de estas características. Yo elegí esta que os presento en esta ocasión porque quería preservar al máximo posible la fisionomía y el sandwich de cubierta.
Tras el fresado de los huecos para los tacos de refuerzo, envuelvo los tacos en tejido de vidrio saturado con resina epoxi, pinto las paredes y base del hueco con generosa resina espesada con microbalones, e introduzco los tacos a presión, retirando la resina sobrante que resulta expulsada por la introducción del taco.
En este caso he dejado los tacos más altos de la cuenta, para facilitar aplicar presión tras la colocación y fácil lijado tras el curado.
Colocación de tubos de goma
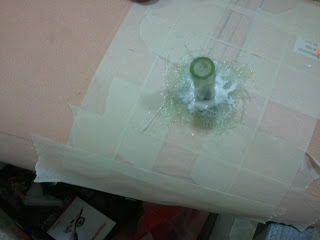
Resina y tejido de fibra...
Final del proceso y a esperar
Hay diferentes maneras de colocar una caja de estas características. Yo elegí esta que os presento en esta ocasión porque quería preservar al máximo posible la fisionomía y el sandwich de cubierta.
Tras el fresado de los huecos para los tacos de refuerzo, envuelvo los tacos en tejido de vidrio saturado con resina epoxi, pinto las paredes y base del hueco con generosa resina espesada con microbalones, e introduzco los tacos a presión, retirando la resina sobrante que resulta expulsada por la introducción del taco.
En este caso he dejado los tacos más altos de la cuenta, para facilitar aplicar presión tras la colocación y fácil lijado tras el curado.
Y después de lijar
A continuación, fresado de hueco para las cajas, incluyendo el fresado hasta cubierta de los huecos para la prolongación de las cajas
Presentación de las cajas de aletas en su sitio...
Envoltura de las cajas con tejido y resina, pintado de los huecos con resina muy espesada con microbalones, para evitar el excesivo descuelgue por gravedad, sellado de la cubierta con cinta de carrocero, e introducción de las cajas en su sitio, cuidando de respetar los tejidos dispuestos en ellas. Para ello, el fresado de la prolongación de las cajas fue cuidadosamente medido, para evitar un ajuste holgado y a la vez permitir la correcta introducción de los cilindros de las cajas.
En este paso, la resina espesada expulsada por las cajas se escapa por ambos lados de la tabla.
La expulsada por carena se retira y la empujada por los cilindros queda atrapada al estar momentáneamente sellados los huecos en cubierta por la cinta.
Una vez colocadas las cajas y verificada su colocación, se retira la cinta en cubierta para dajar escapar el exceso de resina y se vuelve a sellar.
Tras el curado de la resina de este paso, vuelta a la tabla y se retira la cinta de cubierta. Con la ayuda de un cutter se retira fácilmente el pequeño tapón de resina atrapado a esta en la superficie.
Con la ayuda de un tubo trozo de tubo de goma de grosor apropiado, concretamente del mismo tipo que utilizo para la bomba de vacío, y que tiene un diámetro prácticamente idéntico a los huecos de los cilindros de las cajas, ayudo a formar la continuación de estos cilindros de las cajas hacia cubierta.
1- Pintado con resina espesada el interior de los huecos, introduccíón de los tubos de goma previamente encerados con cera para madera, colocación de varios recortes de tejido de vidrio previamente agujereados en su centro, ensartándolos en el tubo hasta agolparlos en el hueco, repaso con resina espesada y a esperar.
Los tubos de goma se ayudan a mantener en una posición rígida con ayuda de un par de destornilladores.
Colocación de tubos de goma
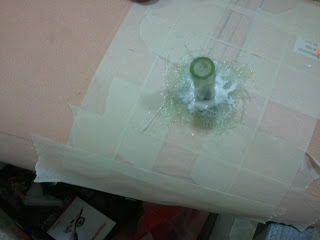
Resina y tejido de fibra...
Final del proceso y a esperar
Tras el curado de la resina, se retiran los tubos de goma, que al estar encerados salen fácilmente con pequeñas torsiones con la mano hasta despegar la pequeña adhesión, y se lija la superficie de cubierta para adecentar el resultado, que resulta ser éste:
En carena, se lijó y repasó el material sobrante, quedando terminada
El próximo día hablamos de la popa. Aunque se puede apreciar que ha sido modificada, aún no está terminada.
Y a falta de ultimar la popa (le queda un sandwich), este es el aspecto de la tabla casi lista para laminar de nuevo.
viernes, 9 de diciembre de 2011
Caja de mástil y straps
Un paso relativamente fácil. Se trata simplemente de fresar los huecos, embutir la caja de mástil y los straps con tejidos de refuerzo y resina espesada, y colocar en su sitio a dejar curar. La colocación no es tan delicada como la de las cajas de aletas, donde prima la perfecta alineación.
Con las mediciones ya realizadas de antemano, en el caso de la caja de mástil se trata de fresar el taco de refuerzo. En el caso de los straps, no considero necesario añadir ningún taco, aunque eso sí, como hemos visto anteriormente, en las zonas donde irán colocados existe un doble sandwich de pvc, lo que da más consistencia al conjunto.
Detalle del fresado de los straps delanteros, donde se puede apreciar el doble sandwich
Detalle del fresado del strap trasero
Preparación del siguiente paso: recortes en fibra de vidrio 160g para embutir los tacos de straps, y doble recorte rectangular en fibra de vidrio 166g y carbono 200g para embutir la caja de mástil.
Protección de la zona de trabajo.
Detalle de caja de mástil
Detalle de straps delanteros
Detalle de straps traseros.
Tanto los straps traseros como los delanteros se ha colocado con doble tornillo, dejando en este caso una sola posición para estos, en lugar de colocarlos paralelos al eje de crujía, donde con el mismo taco se consiguen dos posiciones para poder alternar, pero repartiendo entre dos puntos las fuerzas ejercidas sobre los tacos y asegurando la colocación de los footstraps.
Con las mediciones ya realizadas de antemano, en el caso de la caja de mástil se trata de fresar el taco de refuerzo. En el caso de los straps, no considero necesario añadir ningún taco, aunque eso sí, como hemos visto anteriormente, en las zonas donde irán colocados existe un doble sandwich de pvc, lo que da más consistencia al conjunto.
Fresado para la caja de mástil. Se aprecian huecos en el taco de refuerzo, realizados además oblicuamente para mayor sujeción caja/taco.
Detalle del fresado de los straps delanteros, donde se puede apreciar el doble sandwich
Detalle del fresado del strap trasero
Preparación del siguiente paso: recortes en fibra de vidrio 160g para embutir los tacos de straps, y doble recorte rectangular en fibra de vidrio 166g y carbono 200g para embutir la caja de mástil.
Protección de la zona de trabajo.
Resultado, tras lijar para eliminar el tejido y la resina sobrante que queda sobre la cinta y retirar ésta.
Detalle de caja de mástil
Detalle de straps delanteros
Detalle de straps traseros.
Tanto los straps traseros como los delanteros se ha colocado con doble tornillo, dejando en este caso una sola posición para estos, en lugar de colocarlos paralelos al eje de crujía, donde con el mismo taco se consiguen dos posiciones para poder alternar, pero repartiendo entre dos puntos las fuerzas ejercidas sobre los tacos y asegurando la colocación de los footstraps.
jueves, 8 de diciembre de 2011
Twin...Quad
Como creo haber comentado anteriormente, lo que inicialmente iba a ser un twin, se convirtió con alguna modificación en lo que será un Quad.
Aquí os presento las aletas laterales, para las que finalmente, después de sopesar varias opciones, me decidí por cajas Minituttle.
Aquí os presento las aletas laterales, para las que finalmente, después de sopesar varias opciones, me decidí por cajas Minituttle.
Mediciones para la colocación de las cajas y refuerzos
Y fresado para insertar los tacos de refuerzo, que decidí llevar cuadrados hasta rozar el pvc de cubierta por su parte interior.
Las cajas serán colocadas ligeramente anguladas, como lo está el fresado respecto a la línea de crujía, y quizá alguno extrañe la posición de las cajas laterales respecto a las twin. Hay que tener en cuenta la longitud de las cajas twin, y que la tabla está estudiada para funcionar como twin/quad independientemente, jugando además para esto con la posición de las quillas twin dentro de sus cajas.
lunes, 5 de diciembre de 2011
PVC cubierta
Acostumbro a usar el móvil para tirar las fotos de los procesos. En este caso no tengo fotos de los pasos seguidos, debido a que estuve unos días sin móvil por darle un bañito en una sesión, al fallar el Aquapack.
En cualquier caso, la cosa fue así:
Preformado del perímetro de la plancha de PVC con calor, laminado de 160gr preimpregnado sobre la mesa, ligera impregnación de la cara interior del pvc, sobre todo los bordes, y colocación del pvc cuidadosamente, incluyendo los añadidos de proa y popa.
Bien encintado todo con cinta de carrocero y de embalar antes del vacío, para asegurar la colocación y correcta adhesión.
Embolsado, vacío, y posterior desembolsado.
Tras esto, repaso general a lija manual, retirando el pvc superpuesto en carena y reshapeando los cantos y raíles.
Resultado:
Carena (debo subsanar unos pequeños desperfectos en el pvc, casi en la popa, que me traje al retirar la cinta y el pvc solapado con más prisas y menos cuidado del que debía. Nada importante, teniendo en cuenta además que la popa va a sufrir alguna modificación prevista. Se puede apreciar en la foto).
En cualquier caso, la cosa fue así:
Preformado del perímetro de la plancha de PVC con calor, laminado de 160gr preimpregnado sobre la mesa, ligera impregnación de la cara interior del pvc, sobre todo los bordes, y colocación del pvc cuidadosamente, incluyendo los añadidos de proa y popa.
Bien encintado todo con cinta de carrocero y de embalar antes del vacío, para asegurar la colocación y correcta adhesión.
Embolsado, vacío, y posterior desembolsado.
Tras esto, repaso general a lija manual, retirando el pvc superpuesto en carena y reshapeando los cantos y raíles.
Resultado:
Carena (debo subsanar unos pequeños desperfectos en el pvc, casi en la popa, que me traje al retirar la cinta y el pvc solapado con más prisas y menos cuidado del que debía. Nada importante, teniendo en cuenta además que la popa va a sufrir alguna modificación prevista. Se puede apreciar en la foto).
viernes, 2 de diciembre de 2011
Suscribirse a:
Entradas (Atom)